Stay updated on news, articles and information for the rail industry
May 2025
Rail News: Mechanical
Technology update: Fuel management 2025
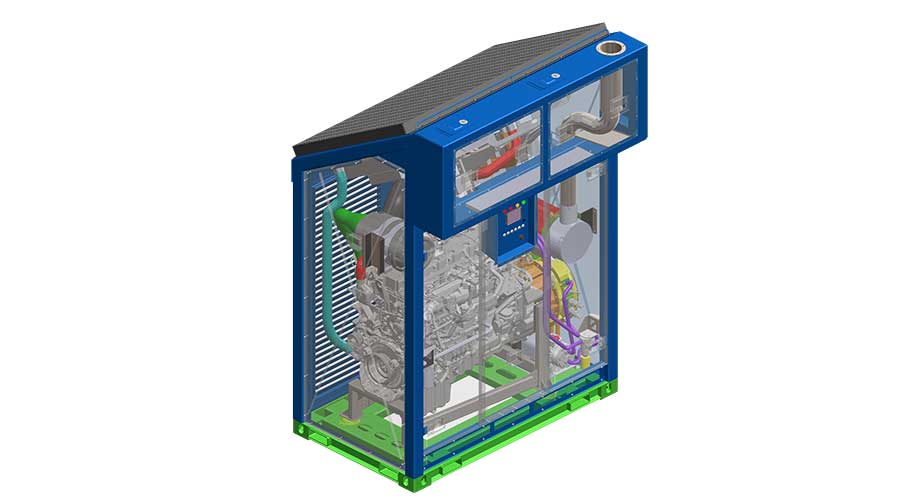
Compiled by Julie Sneider, Senior Editor
OptiFuel Systems
OptiFuel Systems designs and manufactures advanced modular locomotive power systems, offering both new locomotives and repower services engineered to reduce fuel consumption in freight-rail operations by 30% to 40%, OptiFuel officials said.
Leveraging hybrid-electric propulsion and a proprietary variable-speed generator within each self-contained power module, OptiFuel optimizes energy efficiency across a wide range of load profiles for both switch and line-haul applications. The platform supports multiple fuel configurations, including diesel, renewable natural gas and dual fuel.
OptiFuel power systems are configured to align real-time output with operational demand, minimizing idling and part-load inefficiencies. An intelligent power management system continuously monitors grade, load and duty cycle, dynamically allocating energy across sources to maintain optimal performance.
At low throttle settings — such as switching or yard movements — locomotives operate exclusively on battery power in Notch 1 and Notch 2, where fuel-based systems are least efficient, eliminating fuel use during these phases.
At higher throttle levels, high-efficiency engine technologies engage, with battery and engine power working in tandem to preserve tractive effort and responsiveness. Regenerative braking captures kinetic energy and stores it in onboard batteries, redeployed during acceleration or peak-load intervals to further reduce fuel draw.
OptiFuel’s modular architecture supports rapid installation and flexible configuration, minimizing operational disruption and enabling broad deployment, company officials said. Designed with cost-sensitivity in mind, the systems offer a 30-year operating life at a capital cost that supports near-term return on investment, according to OptiFuel.
Hotstart Inc.

Hotstart auxiliary power units (APU) and shore power engine heaters are utilized when a locomotive is parked and idling, whether in the yard or at a remote location. These systems help maintain the prime mover fluids at optimal operating temperatures during cold weather conditions, along with charging the locomotive batteries, company officials said in an email.
Installing such aftermarket equipment greatly reduces unnecessary locomotive idling, resulting in increased fuel savings and reduced wear-and-tear on engine components. Furthermore, using a Hotstart system to keep locomotives warm eliminates issues such as wet stacking and reduces automatic engine start/stop-related restarts, they said.
The APU runs on diesel fuel sourced from the locomotive, consuming an average of 0.5 gallons per hour. This is a significant reduction compared to the locomotive’s standard consumption of four to five gallons per hour, Hotstart officials said. The APU does not require shore power, allowing it to be utilized remotely, they added.
Shore power systems use existing yard electricity, eliminating the need for diesel fuel during idle periods. These electric systems are simple, yet robust, with minimal maintenance requirements, Hotstart officials said. The company supplies numerous configurations and heat outputs, providing an idle reduction solution for most locomotive applications.
Wabtec Corp.

Fuel management is a critical aspect of a modern railroad’s operations. Wabtec’s Trip Optimizer™ (TO) is an industry-leading solution, offering advanced technology to enhance fuel efficiency and reduce emissions, company officials said. There are more than 12,000 locomotives using TO, with 19 customers on five continents, including all North American Class Is, according to Wabtec.
TO functions as a smart cruise control system for trains, considering terrain, train makeup, speed restrictions and operating conditions. Over time, the solution has evolved to handle longer and more complex train makeup, optimizing operations, Wabtec officials said.
Advanced features such as Smart HPT optimize power across the consist, using only the locomotives needed to maintain velocity. TO’s Zero-to-Zero operation lifts stationary trains and stops moving trains at designated control points. The system is EPA-certified to save 10% of fuel burned by a train, with Smart HPT certified for an additional 5% savings, said company officials.
In 2024, Wabtec introduced a significant enhancement in Movement Planner-Pacing. This new feature enhances communication between Movement Planner and TO, resolving previous issues that affected fuel efficiency, Wabtec officials said.
Pacing allows Movement Planner to share its plan with TO, identifying meet events with high dwell times and enabling TO to adjust train speeds accordingly. It minimizes idle time and conserves fuel, without adversely affecting network velocity, Wabtec officials said.
The system provides potential fuel savings of 2% to 4% per dispatch region, reduced idle time and no negative impact on overall network performance, they said.
New York Air Brake LLC

Since 1936, Snyder Equipment, a division of New York Air Brake LLC, has been providing advanced rail support, evolving from steam-era water delivery systems to today’s fully integrated locomotive fueling infrastructure. Snyder’s portfolio includes fuel nozzles, fuel cranes, tank adaptors and vent hoses, pumping systems for receiving and delivering fuel, filter vessels and fuel management systems.
Snyder’s fuel management systems can be configured to track every step of the fueling process. With features such as tank gauging, overfill protection and remote monitoring capabilities, the systems not only improve fuel reconciliation but also enhance safety and operational time, New York Air Brake officials said.
Complementing Snyder Equipment’s fueling technology is the Locomotive Engineer Assist/Display and Event Recorder (LEADER®) system from New York Air Brake. LEADER uses advanced train control and energy management to reduce fuel consumption and in-train forces.
Performing high-fidelity onboard simulations that predict train performance several miles ahead, LEADER® evaluates multiple train operating strategies and selects the strategy that is the best match for increased fuel economy. Deployed on multiple locomotive platforms globally, LEADER delivers measurable savings and emissions reductions, company officials said.
Power Drives Inc.

The patented PowerHouse™ Hybrid from Power Drives Inc. is the newest model in the company’s idle reduction/fuel savings technology lineup.
A U.S. EPA Smartway Verified Technology, the system heats the engine oil and circulates heated coolant through the locomotive engine block and cooling system to maintain a fluid temperature above 100° F, enabling operators to eliminate idling in cold weather. Idling locomotives use five to eight gallons of fuel per hour while the PowerHouse™ uses only 0.38 gallons per hour, company officials said.
The PowerHouse Hybrid model eliminates the need for either shore power or an additional engine as a power source. The model is powered directly from the locomotive battery bank and can run off the locomotive batteries for up to seven days without starting the engine, Power Drives officials said. Alternatively, the Hybrid can be plugged into an external 120 VAC power source and will operate while charging the locomotive batteries.
More stringent regulatory restrictions on emissions, as well as cost savings resulting from reduced fuel consumption, are driving increased demand, according to Power Drives.
“Customer savings have surpassed the investment in as few as three months,” company officials said, adding that typical fuel usage savings in one season surpasses 10,000 gallons.
L.B. Foster Co.
L.B. Foster’s Remote Performance Monitoring (RPM) platform is purpose-built for the unique and demanding needs of the railroad industry’s friction management programs. RPM delivers more than just data — it provides railroads with powerful insights into the performance of entire friction-management programs across multiple divisions, while enabling users to drill down and resolve issues at the system level, L.B. Foster officials said in an email.
This high-level visibility, combined with the ability to track system and program uptime, allows rail operators to identify long-term trends and make smarter maintenance decisions.
But the impact goes far beyond managing FM assets. With optimized FM comes measurable value: RPM-enabled programs drive fuel savings, extend the life of rail assets by reducing wear, and enhance safety, L.B. Foster officials said.
“Our commitment to total friction management — that is, helping customers optimize their FM programs by getting them maximum benefits for minimal costs — goes hand-in-hand with our remote monitoring platform,” said Joel VanderMarel, the company’s senior product manager. “RPM improves the efficiency of your maintenance team, reduces track access requirements, and ensures you get the most out of your investment.”
Since no two railroads are the same, RPM is designed to be as flexible as possible, allowing each user to configure it to display what matters most to them, he said.
“With our powerful reporting engine, we can create custom reports that give our customers exactly the actionable insights they need, when they need them,” said VanderMarel.
ZTR Control Systems

Although fuel is one of the highest operating expenses in rail operations, it’s also one of the most controllable. With rising fuel costs and growing pressure to reduce emissions, effective fuel management is no longer optional. Rail operators need intelligent, data-driven solutions to optimize fuel use without compromising performance, said ZTR Control Systems officials.
That’s where the company’s NexSys comes in, they believe.
NexSys is an advanced locomotive control system designed to optimize fuel consumption through intelligent automation and real-time visibility. At the heart of its fuel-saving capabilities is SmartStart AESS, which automatically shuts down and restarts the locomotive based on operating conditions.
Instead of idling for hours and wasting fuel, SmartStart evaluates key parameters — such as engine temperature, battery voltage, air pressure, and ambient conditions — to determine when it’s safe to turn the engine off, ZTR officials said. It then continuously monitors these metrics to restart the engine when needed, ensuring the locomotive is always ready to operate.
This proven technology can save more than 8,000 gallons of fuel per locomotive annually, significantly lowering fuel costs and emissions, according to ZTR.
Beyond automation, NexSys integrates with the ZTR Vision platform and provides near real-time insights into fuel usage, idle time and performance trends. This empowers railroads to refine fueling strategies, optimize crew practices and schedule maintenance based on real operating conditions, not assumptions, ZTR officials said.
The result? Fewer wasted gallons of fuel, less engine wear and better asset utilization across the fleet, ZTR officials said.
Email questions or comments to julie.sneider@tradepress.com.