Stay updated on news, articles and information for the rail industry
January 2024
Rail News: Mechanical
Keeping the train wheels rolling
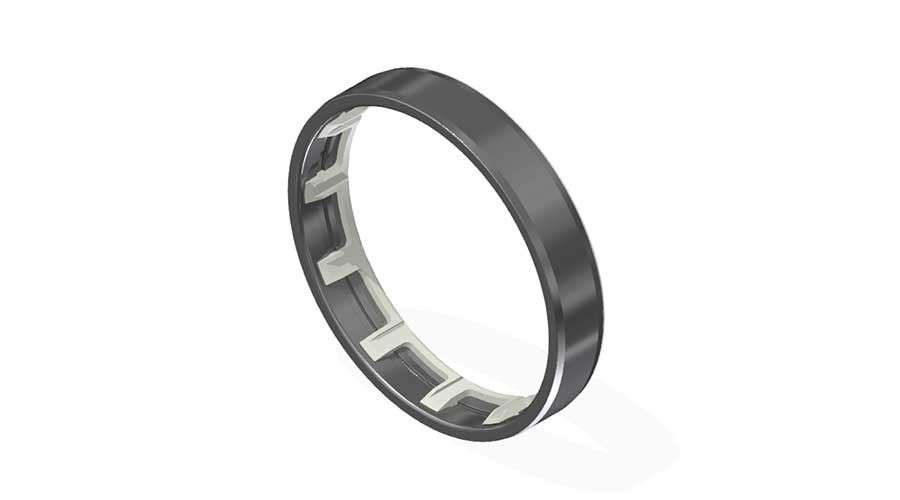
Compiled by Julie Sneider, Senior Editor
Amsted Rail
Amsted Rail’s IBEX™ Truck Mounted Brake System is extra light, balanced and durable, company officials said in an email. In terms of weight, the system averages 802 pounds less than body-mounted brake systems and 220 pounds less than other truck-mounted brake systems, they said.
Adaptable to narrow- and wide-gauge applications, the IBEX features a replaceable, rugged durable design, and a faster and easier beam position adjustment.
The system also offers:
- a maximum shoe-to-wheel alignment and weight balance for better wheel wear balance and longer wheel life;
- uniform shoe force balance for even braking and maximum shoe life;
- a versatile modular design featuring weld-free bolted construction and replaceable brake heads;
- lubrication and seal-free air bag and fewer moving parts for longer brake system life; and
- a beam-mounted slack adjuster with connecting rods for more clearance.
Amsted’s newer products also include the composite Wear Ring 2.0, which is designed to improve axle-journal grooving/wear; and the Model 35770 Group N Hand Brake, which is AAR-approved, available in a long- or short-release lever and designed for high-vibration service.
A. Stucki Co.
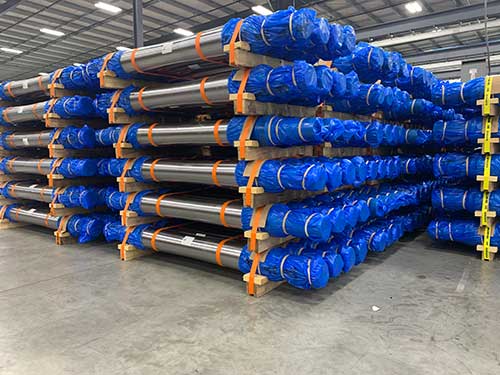
A. Stucki Co. has supplied highly engineered parts and services to the rail industry for more than a century. The company has grown and diversified in recent years to supply dynamic control products, brake system components, springs, bearings, track infrastructure and other products, as well as provide remanufacturing, repair, direct-to-locomotive refueling and additional services.
Headquartered in Pittsburgh, Stucki operates 20 facilities throughout the United States, Mexico and Brazil. Through its four manufacturing divisions, the company provides advanced engineering, manufacturing, fueling and maintenance services to the rail industry.
Some of Stucki’s recent developments include:
- expanded and modernized axle lathe equipment for precision machining of freight-car, transit-car and locomotive axles;
- wheel shop improvements designed to increase efficiencies and output for all sizes of freight-car wheel sets;
- expanded product lines of freight-car brake components and production capacity, including brake beams, hand brakes, brake levers, brake beam liners and brake shoe keys; and
- modernized equipment process improvements for reconditioned freight-car roller bearings and locomotive Hyatt journal bearings.
“The market for high-quality and readily available rail-car parts has been growing,” said Scott Driggers, Stucki’s president of reconditioning and repair services, in an email. “That growth is being driven in part by investment in rail networks and infrastructures in the United States and around the world.”
Improvements in rail-car technologies are not only enhancing the reliability and tracking of goods transportation, but often are doing so in an environmentally friendly way that’s also become a major factor in rail and rail-car parts manufacturing and maintenance, he said.
Knorr-Bremse/Knorr Brake Co.
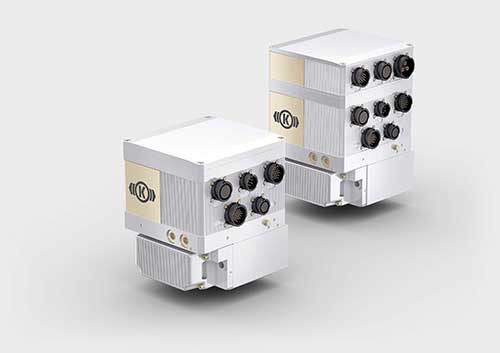
The EP2002 CubeControl braking system from Knorr-Bremse — and its North American transit-rail subsidiary Knorr Brake Co. — is the latest generation of brake control systems for passenger-rail vehicles. It combines a distributed architecture and mechatronic design in one package, company officials said.
The EP2002 mechatronic architecture is setting new standards in advanced brake control around the world, they said.
EP2002 CubeControl integrates brake control and brake management electronics with pneumatic valves for service and emergency braking, and wheel slide protection in a single mechatronic unit for each bogie. EP2002 valves are mounted on a car’s underframe, local to each bogie, to provide increased availability and shorter emergency braking distances.
Currently, Knorr-Bremse’s EP2002 CubeControl system is installed on over 200 rail projects globally, company officials said. More than 100,000 of the systems have been in service daily for more than two decades, they added. In North America, the EP2002 CubeControl system is used on the Los Angeles County Metropolitan Transportation Authority’s HR4000 fleet and will be installed on the Washington Metropolitan Area Transit Authority’s 8000-series cars.
Knorr-Bremse made rail engineering history with the decentralized Brake Control System family originally known as EP2002, company officials said. The rebranded CubeControl family features new functionalities.
A new deceleration control system ensures reproducible braking distances even in rapidly changing conditions, while new ethernet specifications enable condition-based maintenance, Knorr-Bremse officials said. A new Wheel Slide Protection algorithm is designed to reduce braking distances even under extremely low adhesion conditions.
MPL Innovations Inc.
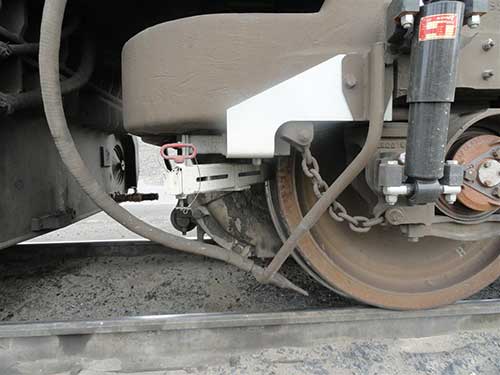
MPL Innovations offers solid stick lubricants for both gauge face and top-of-rail applications. The gauge face technology has been used for over two decades and the top-of-rail product is available after extensive testing at the Transportation Technology Center in Pueblo, Colorado, MPL officials said.
The gauge face interlocking solid stick uses MPL’s patented NatureBlend formulation of biodegradable and renewable plastics as binders and a vegetable oil to provide gauge-face lubrication, in addition to various extreme pressure additives, they said.
The top-of-rail, Topstick material uses a reformulated combination of lubricants to lower the coefficient of friction so a locomotive’s tractive effort isn’t compromised.
This lubricant is fed into a wheel using a constant force spring and is applied to the wheels to condition rail whenever a locomotive is moving — not just in curves as with more common wayside systems, MPL officials said.
MPL NatureBlend stick lubrication and Topstick systems offer reliability and ease of maintenance, they said, adding that the products also provide 2% fuel savings and a 35% wheel-wear reduction. The top-of-rail product uses the same truck frame attachment bracket as the wheel flange lubricators to reduce installation time and cost.
The product is manufactured from renewable and biodegradable components — a win for the environment as railroads strive to reduce greenhouse-gas emissions, MPL officials said.
Southern Technologies Corp.
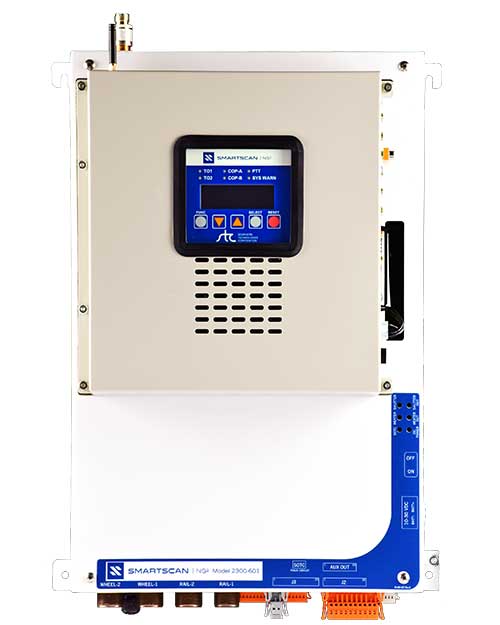
Southern Technologies Corp.’s (STC) defect detectors measure temperatures on rail-car bearings and wheels for all trains that pass over a site. Auxiliary alarms, such as dragging equipment detectors and clearance monitors, can also be monitored by the detectors.
The STC detectors use the Delta temperature method to monitor bearing temperature. Delta temperature provides a consistent bearing health indication regardless of sun, wind, snow or rain conditions, company officials said. Having a consistent temperature measurement over long distances also facilitates more accurate bearing health trending.
If a bearing or wheel has an elevated temperature indicating a failure, the detector radios an automated announcement to alert train crew members of the failed bearing’s location so that they can stop the train, investigate and prevent a potential derailment. The temperatures of all bearings and wheels are also reported to the railroad’s back office for analysis and trending information.
The newest detector in the Southern Technologies’ lineup is the SmartScanNG2, which features bearing and wheel monitoring capability in a single unit, company officials said. It offers an integrated technology for the use of Frauscher Sensor Technology’s zero-speed wheel sensors; an integrated radio and track circuit; front display for easier maintenance and troubleshooting; backward compatibility with previous track hardware and cabling; and robust dual processor architecture for future development capacity.
Email comments or questions to julie.sneider@tradepress.com.